Caterpillar (CAT) engines are known for their power, durability, and reliability. They are essential for heavy-duty equipment in multiple industries, such as maritime, construction, mining, trucking, and agriculture. For optimal engine performance, sufficient oil filtration is essential. The most efficient oil filtration for CAT engines is centrifugal oil filters. In this blog, we will delve into the crucial importance of these filters in maintaining the smooth operation of Caterpillar equipment.
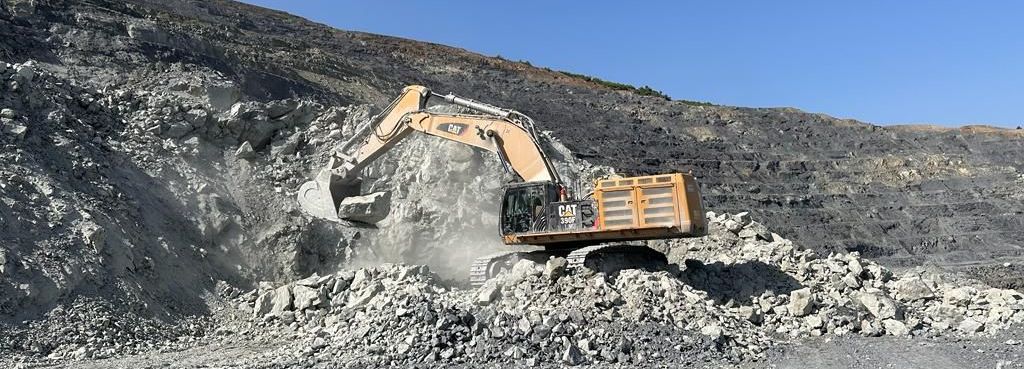
Why Centrifugal Oil Filters are Crucial for CAT Engines
1. Greater Filtration Capabilities
Centrifugal filters use centrifugal force to capture microscopic particles that can easily pass through standard full-flow filters. These tiny contaminants accumulate over time and cause significant wear on critical components. By removing these particles, centrifugal filters reduce degradation and extend overall engine life.
2. Extend Oil Change Intervals
Centrifugal filters are very effective at removing contaminants, which helps keep the engine cleaner for a longer period. By increasing the intervals between oil changes, you can significantly reduce equipment downtime and lower the costs associated with frequent oil changes. This strategic approach not only saves time but also improves overall operational efficiency.
3. Reduce Engine Wear
The accumulation of contaminants in engine oil increases friction between moving parts, resulting in excessive wear and tear. Centrifugal filters help minimize the presence of harmful particles, allowing your engine to run smoothly. This not only reduces wear but also helps maintain optimal performance over time, which lowers the risk of costly repairs or breakdowns.
4. Lower Maintenance Costs
Proper oil filtration is essential for preventing engine damage and is often more cost-effective than repairing worn components. Centrifugal oil filters effectively reduce contaminants in the oil system, protecting critical engine parts. This leads to less frequent maintenance, a lower risk of catastrophic failures, and ultimately reduced maintenance costs.
5. Environmental Benefits
One of the most significant yet often overlooked benefits of centrifugal oil filtration is its positive impact on the environment. This technology extends the lifespan of oil and significantly reduces the frequency of oil changes, which in turn minimizes the generation of waste oil. As environmental regulations become more stringent, companies have a valuable opportunity to improve their environmental footprint by installing a centrifugal filter.
The IOW Group Difference
Installing a standard centrifugal filter on your machinery is not sufficient. Standard technology has remained largely unchanged for over 50 years, making it less effective. In contrast, IOW Group's latest technology enhances separation capabilities by 150%, maximizing its benefits. On average, IOW Group removes twice as much as standard centrifugal filters, which extends oil change intervals, prolongs oil life and increases overall engine life - often by up to three times.
IOW Group Installations on CAT Engines
List of Services
-
CAT 390F Hydraulic ExcavatorList Item 1
An IOW MP090 was installed onto a C18 ACERT Engine to enhance maintenance and longevity of a client's CAT 390F Excavator. Following an initial 700-hour run time, the IOW MP090 achieved an average RPM of 5,800 and sludge thickness of 1mm, removing 475g of contaminants from newly replaced engine oil. The IOW MP090 consistently maintained the optimal properties of the engine's lubrication oil, resulting in extended oil change intervals, reduced maintenance costs asnd enhanced engine efficiency.
-
CAT C280-12List Item 2
A client wanted to upgrade their oil oil filtration technology. They initially had three Mann+Hummel FM200-12 centrifugal filters but these were replaced with three IOW MP200s. The IOW Group centrifugal filters were installed on existing mounts, along with our remote monitoring technology so engineers could monitor performance and be notified when a service is required. After a run time of 506 hours, the MP200s removed 38mm of soot collectively from the engines lube oil.
-
CAT G3608 Natural GasList Item 3
Natural Gas Compression sites put lubrication oils under extreme pressure, with differentiating temperatures and pressures throughout processing. As a result, high levels of contaminants are found in the lube oil system of these CAT G3608 engines. Two IOW MP200 centrifugal filters were required to clean the oil efficiently. Results showed a significant improvement in oil cleanliness, with ISO codes improving from 22/19/11 to 18/16/13.
-
CAT 3406 - Trucking InstallationList Item 4
A 2015 Kenworth W900L truck required an IOW MP090 centrifugal filter with a pressurized drain system (PDS) to be mounted onto the frame rail where the inlet/outlet hoses were securely fastened to avoid moving parts. Initial ISO codes before the IOW MP090 instllation were 21/18/12. After 3 months, the ISO code improved to 19/17/12.
-
CAT 3208 Installation
IOW Group retrofitted a CAT 3208 with an IOW MP090 Centrifuge and CentriClean SCU003 Monitor. Due to the limited space in the engine room, the MP090 was installed above the engine for gravity drain.
-
CAT 3516C Engine
An IOW MP200 Centrifugal Filter was retrofitted onto a CAT 3516C engine along with a CentriClean SCU003 monitor.
-
CAT 3612
IOW Group replaced 3x Mann + Hummel FM200 Centrifuges with 3x IOW MP200 Centrifugal filters. This installation was simple and straightforward, as IOW Group's Centrifugal filters have been designed to simply bolt-on, bolt-off in place of old technology.
-
CAT C15 Acert
IOW Group replaced a Spinner II 560HE with an IOW MP090 Centrifuge, along with a CentriClean SCU003 Remote Monitoring System. Before the upgrade, the client was changing thier oil every 15,000 miles driven, but with an IOW MP090, they were able to increase the oil change intervals to 36,000 miles.

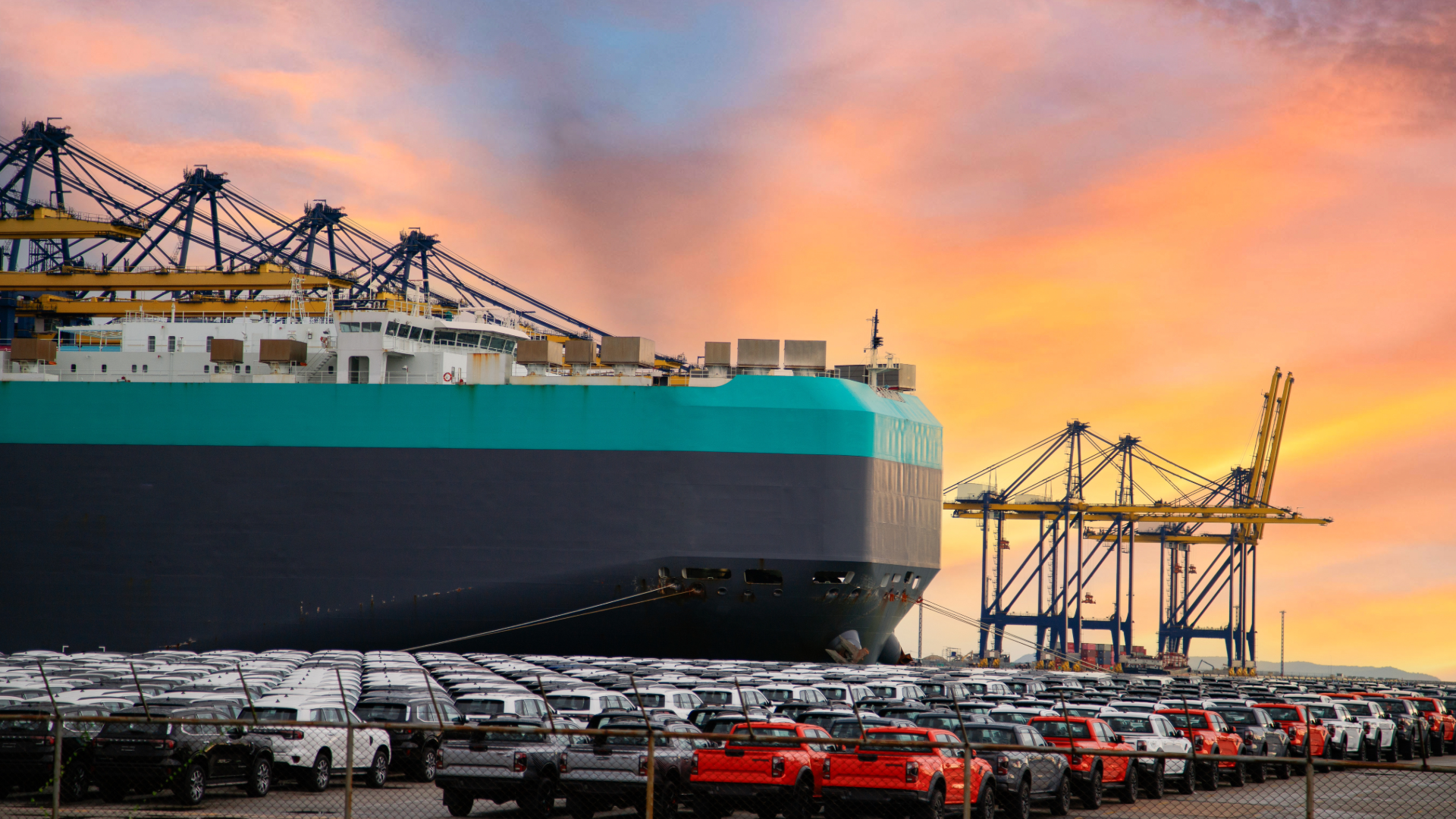
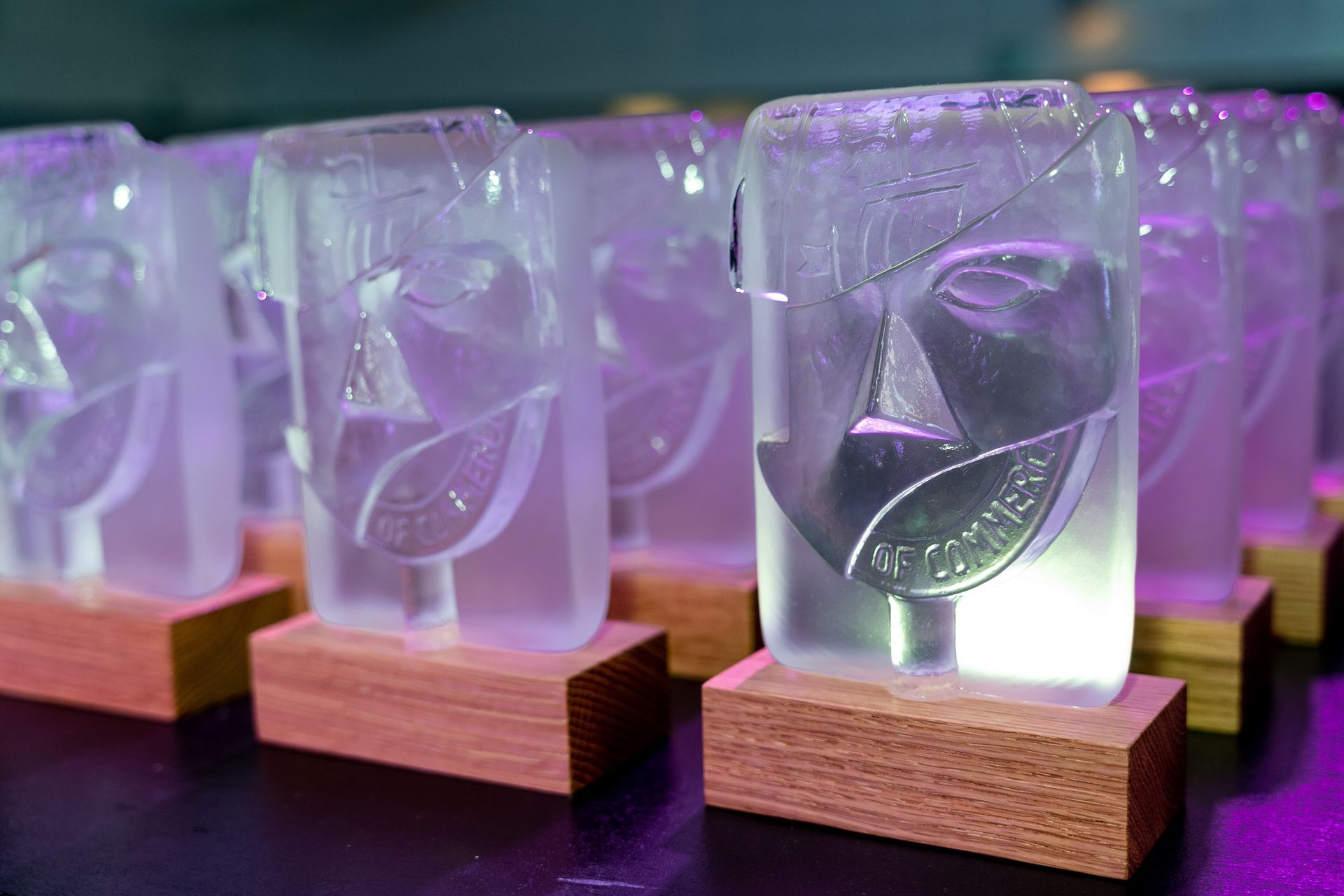
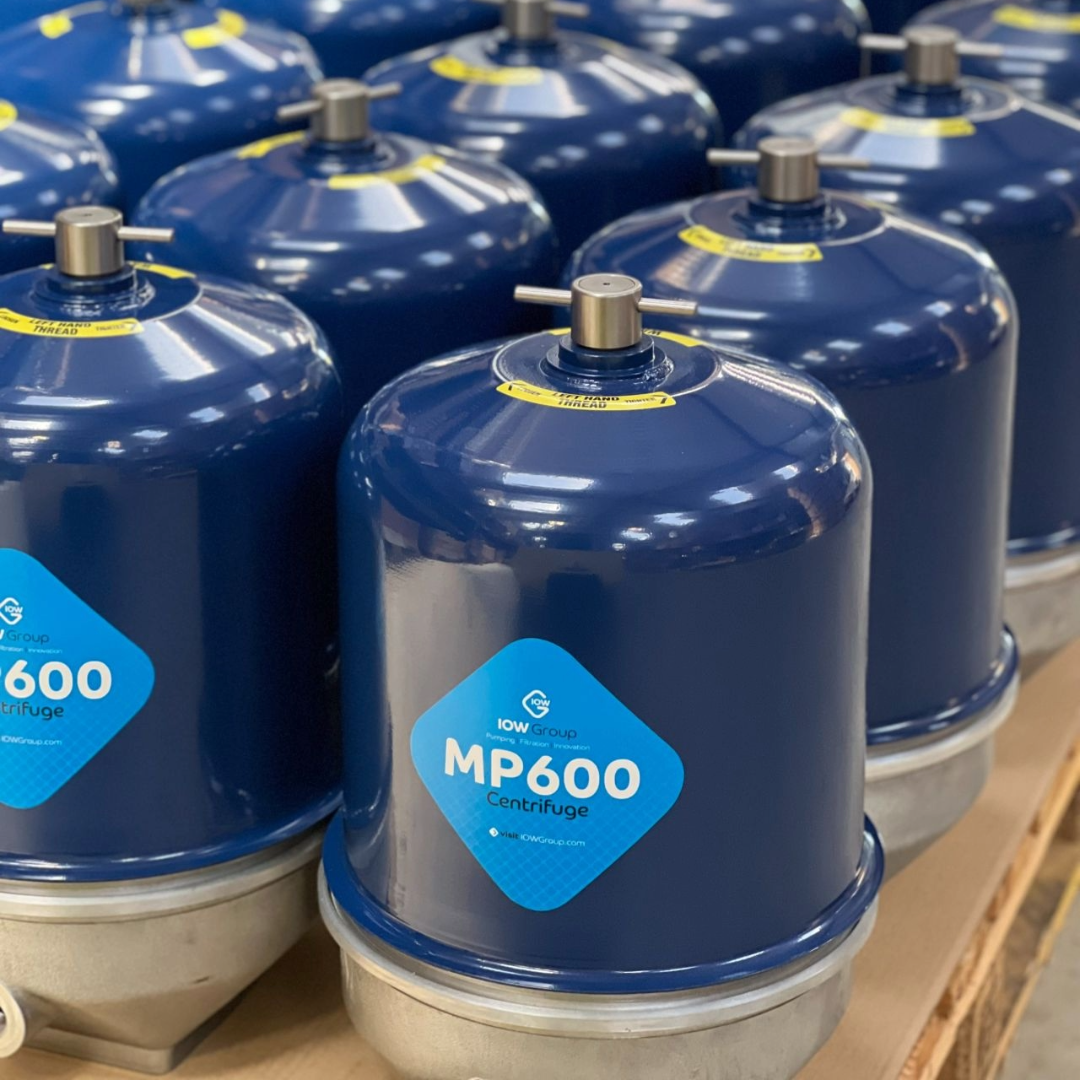