Industry: Marine
Engine Type: MAN 9L21/31
Model Installed: IOW MP600 centrifuge filter
Background
CMA CGM approached us eager to make cost efficiency savings on one of their container ships 'ANL Wangaratta'. They had an MAN 9L21/31 engine running at 5 bar pressure and with an oil volume of 1100 liters. It was decided the best model for them would be the IOW MP600 centrifuge filter. By choosing to upgrade their filtration system to an IOW centrifuge they were picking the best filtration technology currently available with many long term benefits. The results did not disappoint with the IOW MP600 centrifuge filter removing more than 2.5 times the amount of contaminants than the old setup and some surprising outcomes from this installation.
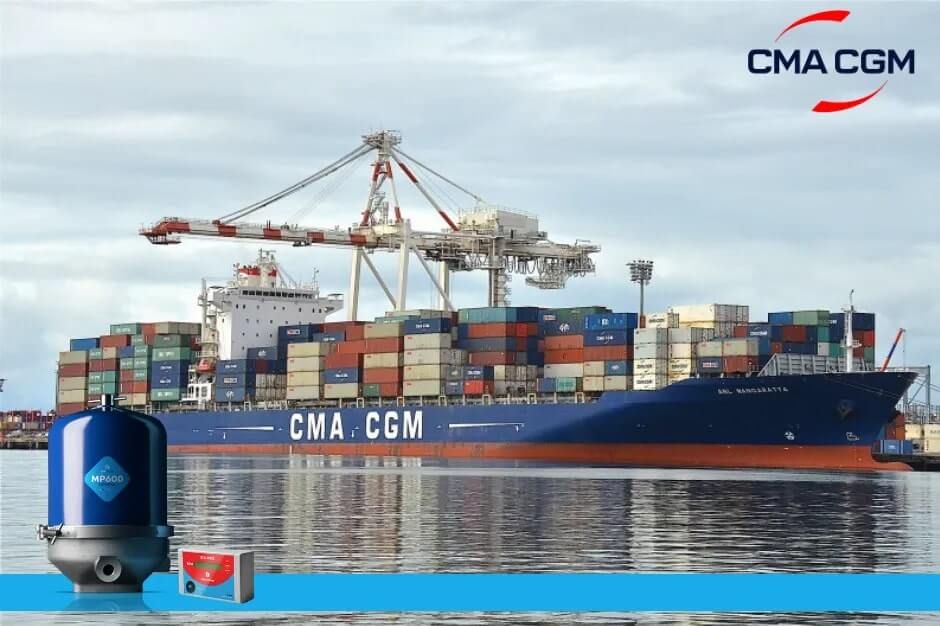
An IOW MP600 centrifuge filter was installed onboard a CMA CGM vessel
Installation
The IOW centrifuge filters have all been designed to retro-fit to existing pipework to make upgrading your filtration system so easy. On this installation the IOW MP600 centrifuge filter was fitted on the existing centrifuge filter bracket that is available with an MAN 9L21/31 engine as standard. Changing the centrifuge over to the IOW MP600 centrifuge filter was a quick and simple process.
As quickly as it was installed, the fantastic results started showing! The combination of bowl disc technology, remote monitoring, and the unique design features of the IOW centrifuges combine to create huge centrifugal force and get these great results for our customers. These features are patent protected and only available through IOW Group, helping it be 150% more efficient than any other product currently available.
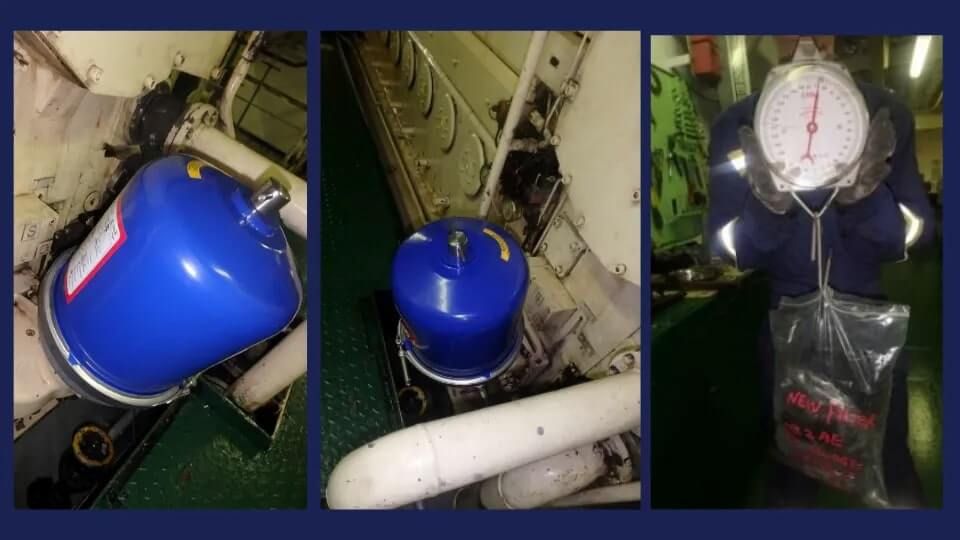
When installed the IOW centrifuge filter removed 2.5 times more sludge from the lube oil.
The Results
After 136 run hours the IOW MP600 centrifuge filter had removed a massive 6kg of sludge from the lube oil! That works out at 2.5 times more contaminants removed than what the old filtration technology was capable of. The previous old centrifuge filter collected only 2.5kg of sludge over the same time period.
The IOW MP600 centrifuge filter was installed with a remote monitoring unit (SCU) that illustrated that the centrifuge was turning at 4530 RPM. The faster the bowl speed, the more effective the separation process. An IOW centrifuge filter spins 15-30% faster than other market-leaders, which helps draw out much more harmful particles from the oil. The IOW centrifuge filter range are the only self-monitoring centrifuge filters in the world, so we were unable to measure the performance of the old centrifuge brand. The monitoring units (SCUs) that the IOW Group offer come in two models, each with different features. However, both have the same advantage by measuring, recording, and monitoring performance, you can ensure your centrifuge filter is performing optimally, plan maintenance accordingly, and investigate any changes in performance. Find more about the SCU (separator control units) control panel here.
Customer Feedback
CMA and the crew of ANL Wangratta were pleased and impressed with the results that the IOW centrifuge filter produced. Collecting over 2.5 times more sludge over the same time period making it 140% more efficient overall. The question now was...what was contained in this soot that had not been filtered out previously?
The only solution to this question was to an conduct oil analysis on the contaminants removed to find out what it was made up of.
It was also determined that due to the effective filtration, the lubrication oil was suitable for continued use and particulate levels were low - all thanks to the IOW centrifuge filter.
Conclusion
Lube oil analysis and testing of the IOW centrifuge filter sludge cake showed high levels of asphaltenes. The soot removed from the centrifuge filter could have been extremely harmful and costly in the long run.
Asphaltenes are naturally occurring in crude oil. They are large, complex, and heavy carbon molecules and one of the most common foulants in the industry- they contain hundreds or even thousands of chemical species, and are insoluble.
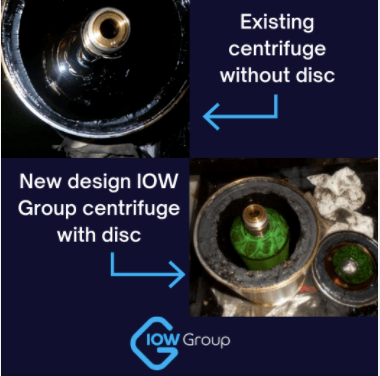
Bowl discs inside IOW Group centrifuge filters assist with finer separation
Asphaltenes are particularly problematic with regards to corrosion and fouling in an engine, and the deposits of these create process inefficiencies, deteriorate equipment rapidly, and as a results, increase maintenance expense and a loss in production levels. To avoid the deposition of these particles in the equipment they must be efficiently removed.
The IOW MP600 centrifuge filter successfully highlighted and contained the harmful contaminants, avoiding further damage. Through investigation of the sludge collected in the centrifugal separator, engineers were able to diagnose and identify the source of the problem correctly. Without this intervention, the massive quantities of particulate would have caused increased engine wear, maintenance, and overhaul costs in the future.
IOW Group was happy to assist in resolving this ingress of asphaltenes and helping to optimize reliability, productivity, and efficiency onboard this vessel by using an IOW centrifuge filter. By moving away from old centrifugal technology and opting to upgrade to an IOW centrifuge filter, CMA has extended the life of their engine and lube oil.
Interested in upgrading you filtration system?
Fill in the contact form below and one of our team will be in touch
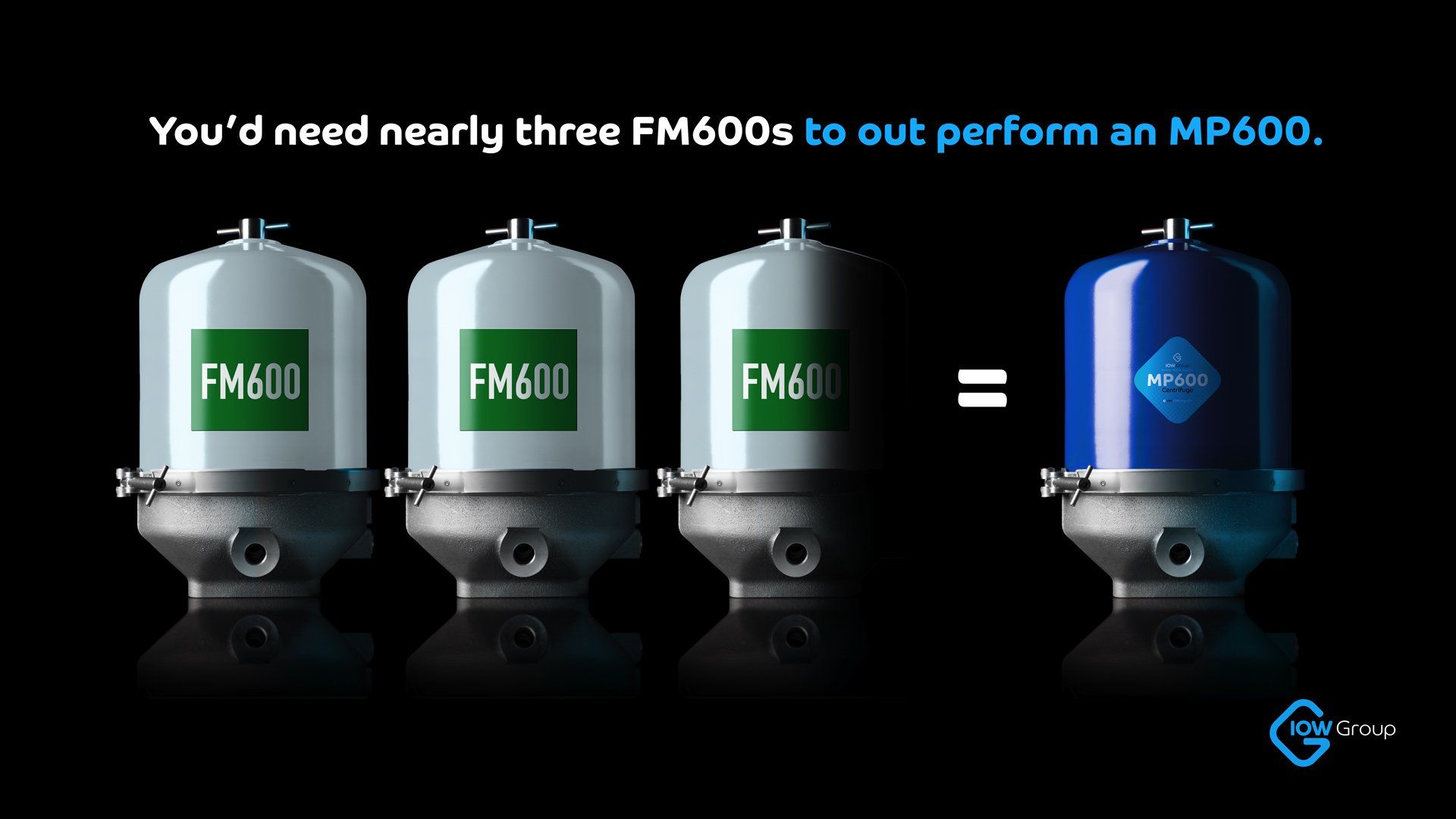
An IOW centrifuge filter out performs competitors by almost x 3!

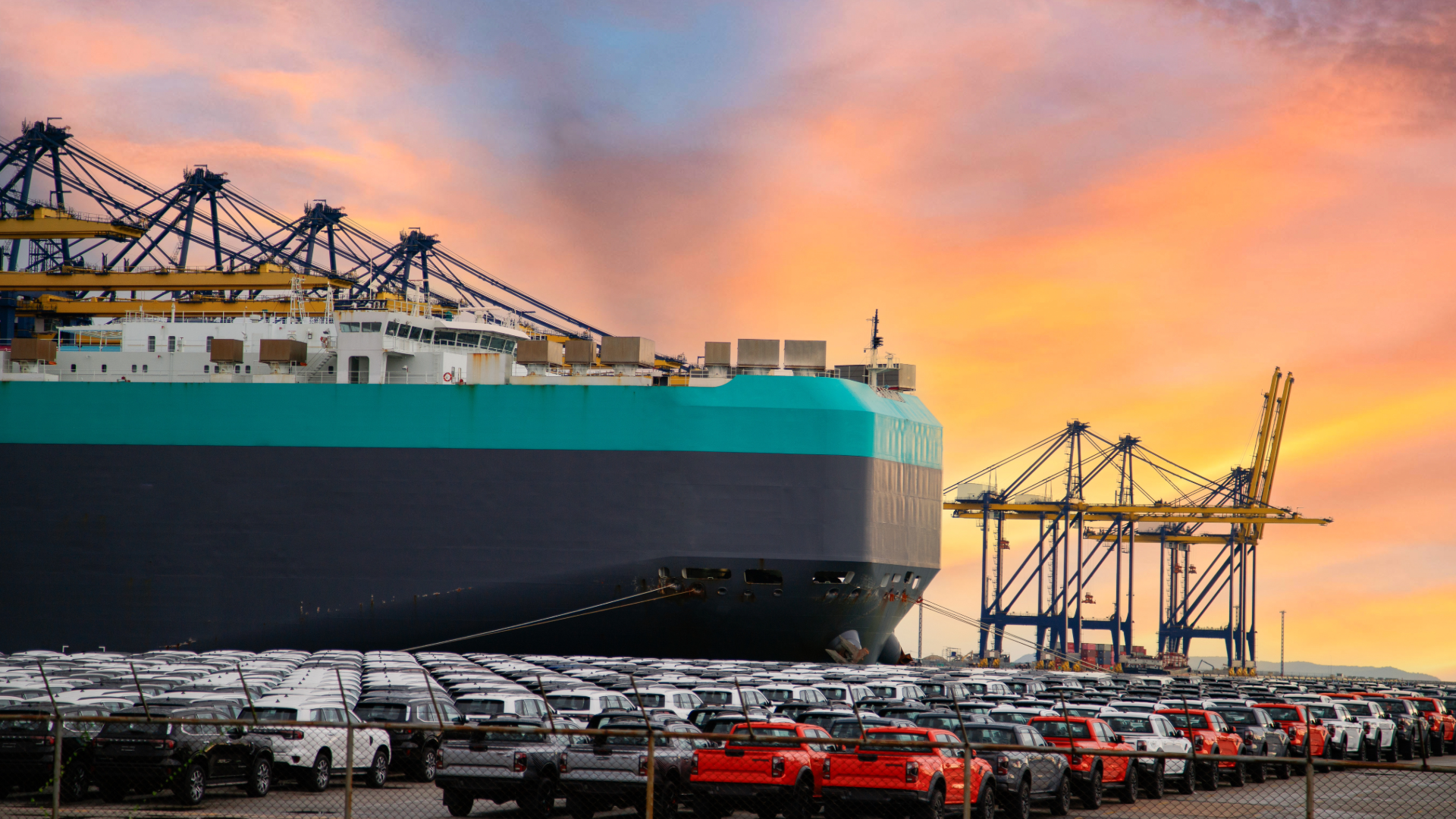
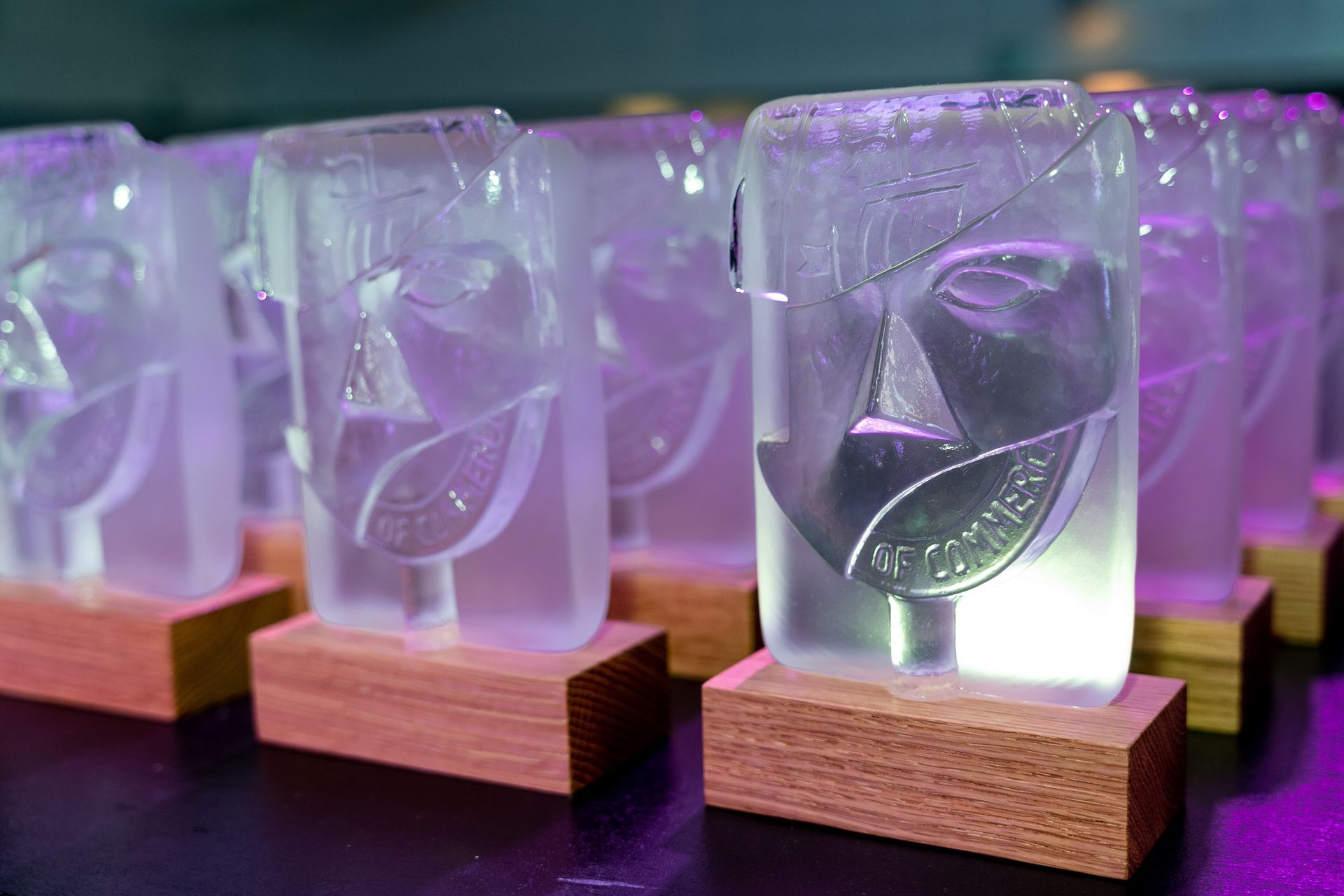
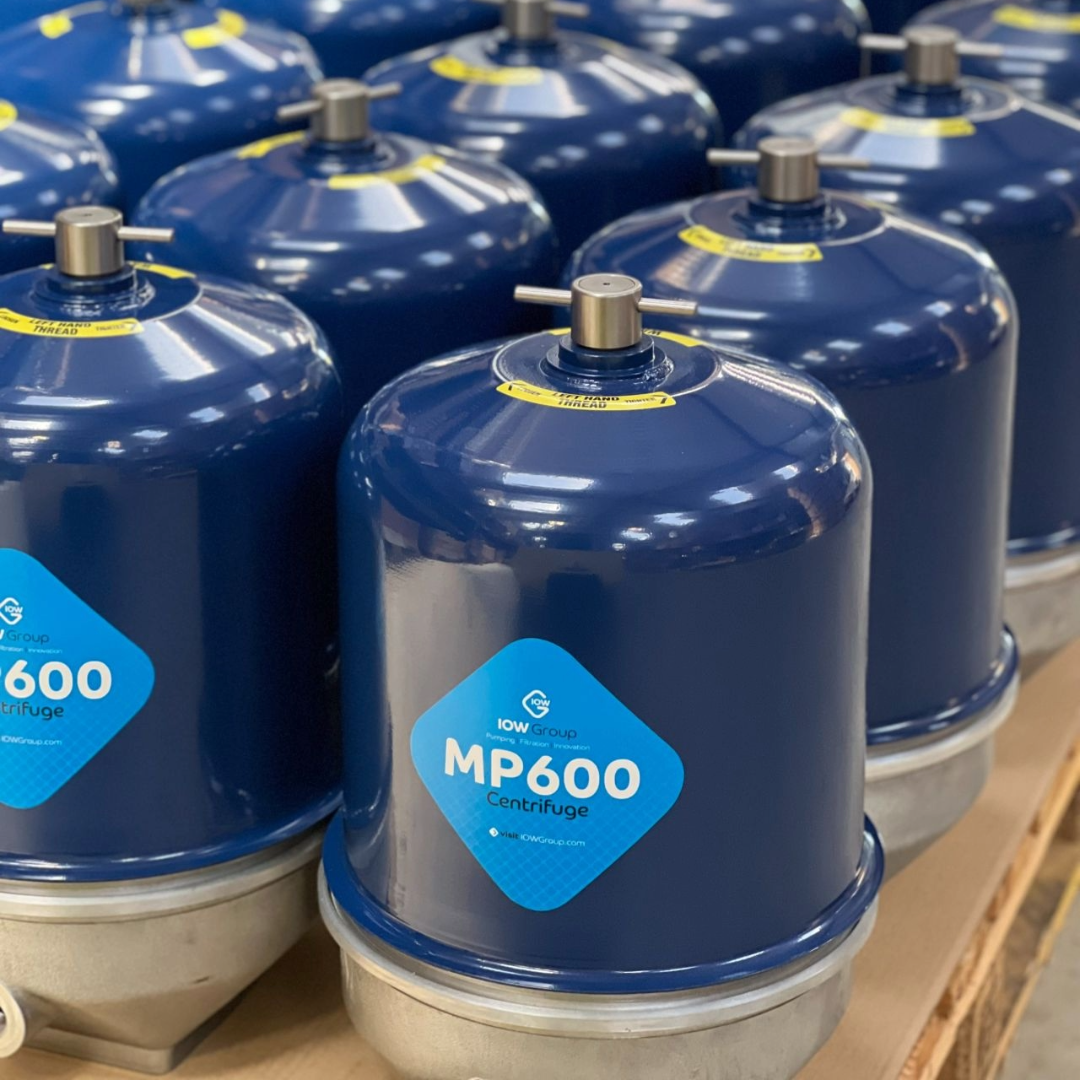