Overview
A client upgraded an old FM600 centrifuge to the IOW MP600 centrifuge and observed a remarkable difference in performance. IOW Group’s range of centrifugal filters outperform any other centrifuge of its size on the market. This is the result of cutting-edge technology, featuring bowl discs and distributor impeller, along with the capacity to achieve higher RPM for enhanced separation.
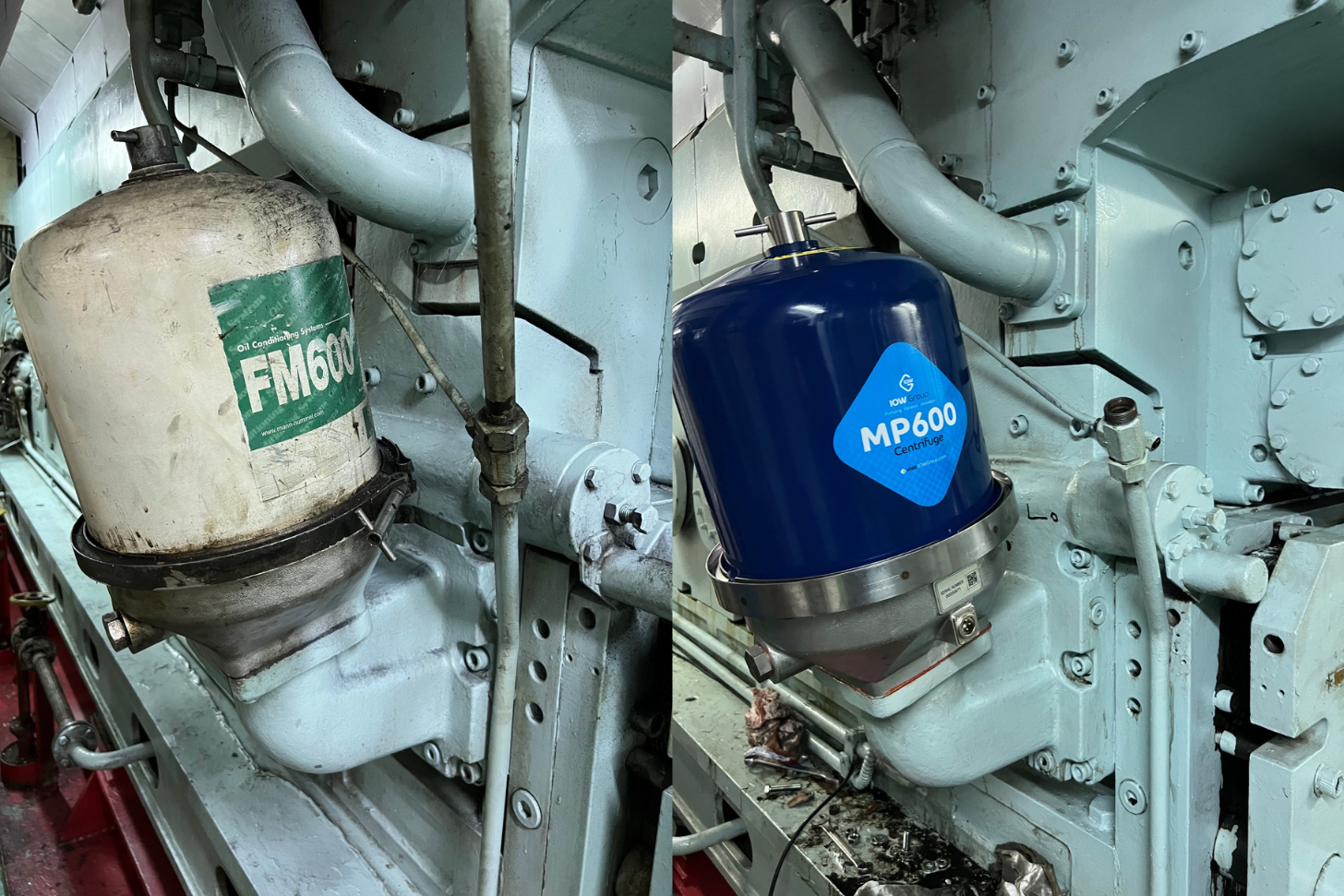
Installation
An IOW MP600 was simply installed onto the MAN 8L 27/38 engine with a bolt-off, bolt-on retrofit design. An SCU 0002 control unit was also integrated into the installation to monitor the MP600’s performance. This monitoring unit provides real-time RPM readings, tracks operating hours, and alters operators when maintenance is needed. The MP600 achieved 4,500 RPM, enhancing its separation capabilities.
Results
The MP600 retrofit delivered impressive results, effectively removing 35mm sludge after 270 hours of operation. Following the trail, the customer decided to keep the IOW MP600 installed on their MAN 8L27/38 engine. With remote monitoring, engineers were notified when a clean was needed and can monitor the performance of the centrifuge.
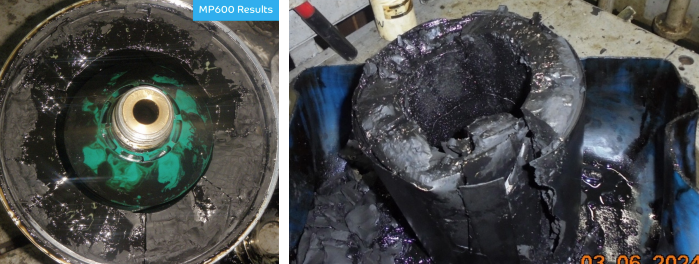
Conclusions
Removing significant amounts of sludge from the engine’s lubrication oil helps maintain a cleaner and more efficient engine. This process brings multiple benefits to operations, including:
• Reduced wear on critical components
• Extends the lifespan of the engine
• Increased oil change intervals
By preventing sludge build-up, you can avoid costly repairs and premature engine failure through reduced maintenance needs. Improved fuel efficiency also means lower fuel expenses overtime. Furthermore, a well maintained engine requires fewer oil changes and maintenance services, ultimately reducing costs on routine upkeep, making IOW Group centrifugal filters a great investment with high ROI.
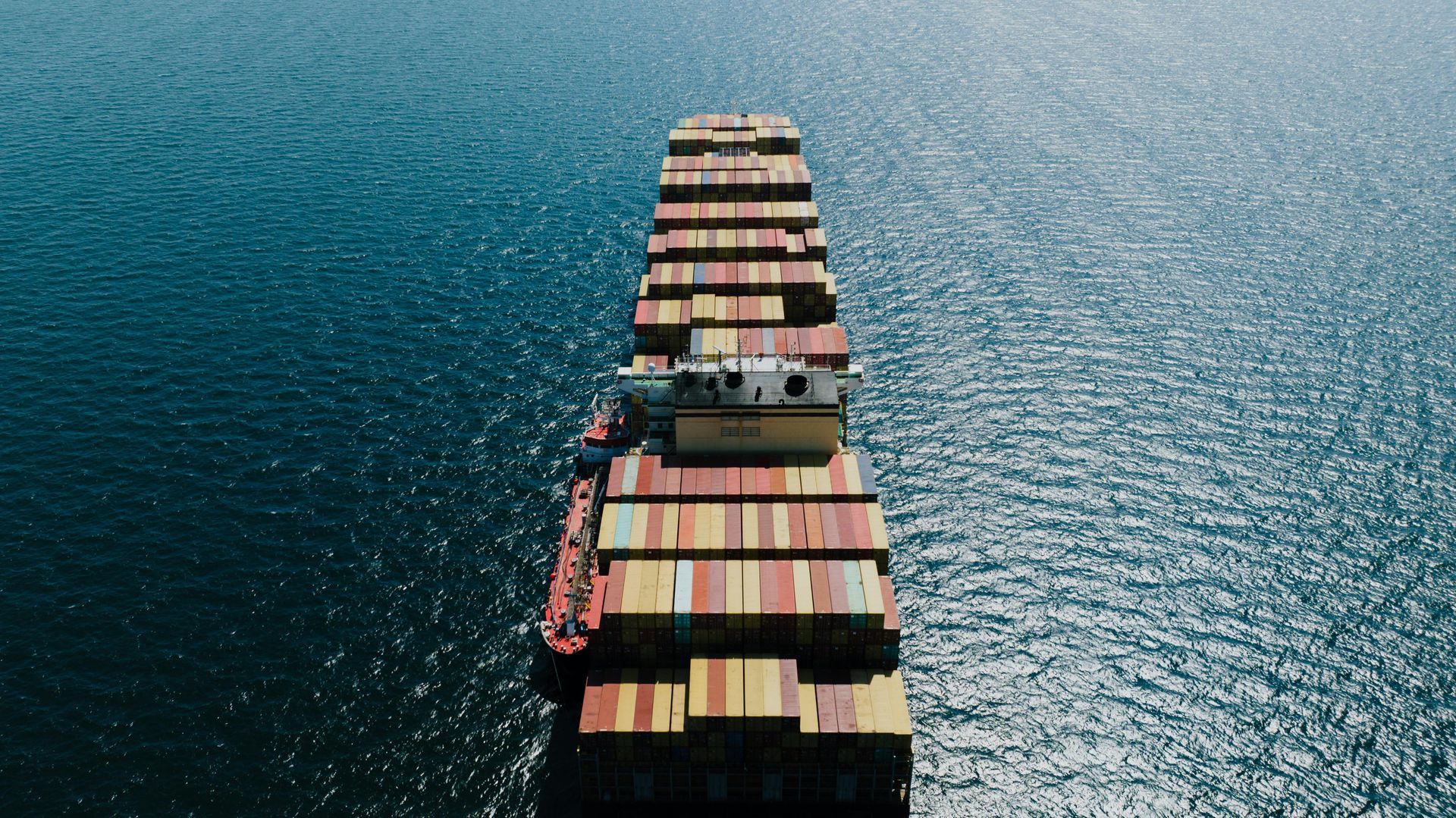
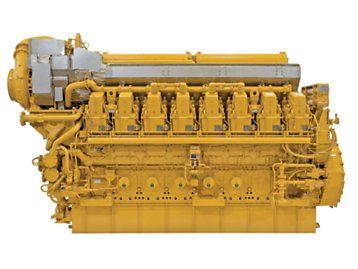
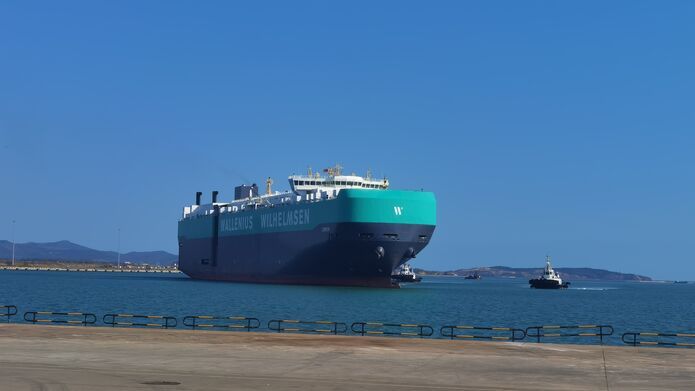