We all know contaminants in lubrication oil cause damage to your engine and its components. These particles can have a catastrophic impact on your engine lifespan. Microparticles are often already present in even brand new engine oil, and bad storage techniques add to the contamination. A number of environmental factors mean these particles enter the engine and into the lubricating system. The question is, how can we protect our engines from these killers?
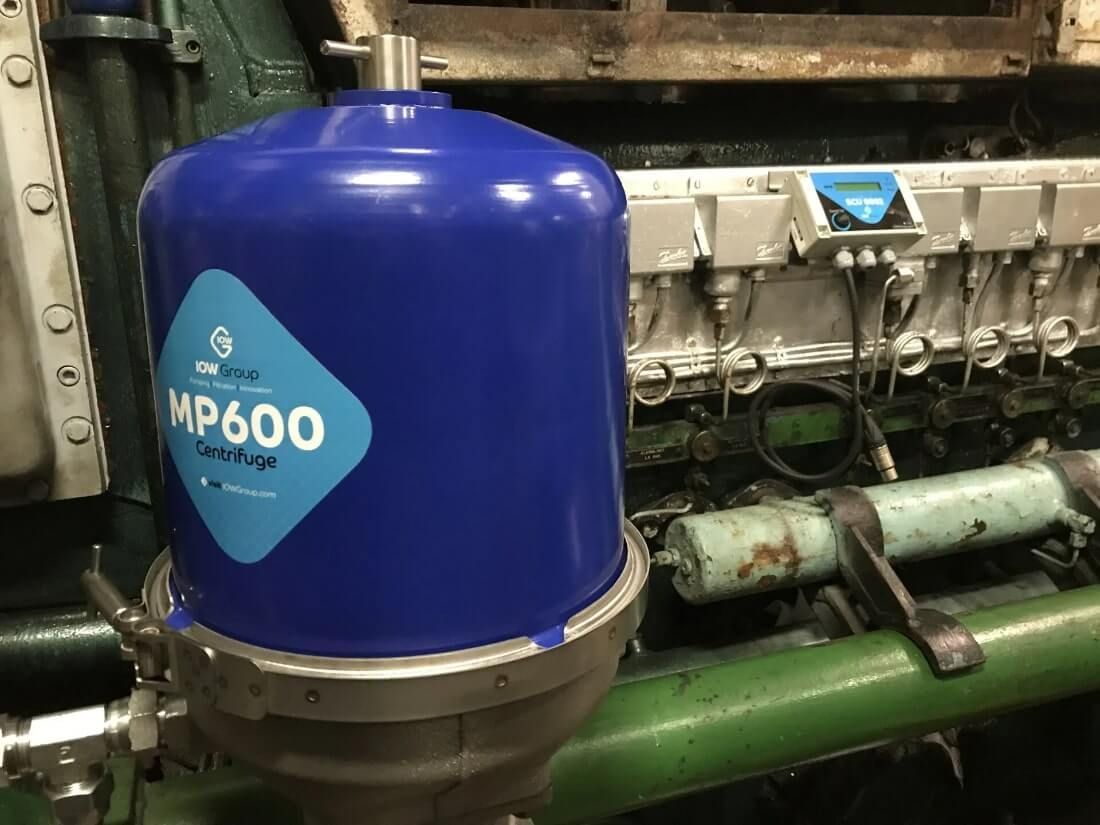
Contaminants in lubrication oil are unavoidable but can be managed with the help of an effective filtration system or centrifuge filter
Oil centrifuge filters have been used for a long time in the maritime industry to filter mineral oils. Centrifugal oil separators are seen as the most efficient way to remove contaminants. Centrifugal oil separators collect the soot particles on a paper insert inside the bowl. The paper is easily removed during cleaning and is the only consumable item. With a centrifuge filter, you do not need to purchase expensive replacement filters, making it an economical choice.
Sea-going vessels use huge amounts of lube oil and the cleaning of this oil is paramount to the smooth running of these reciprocating engines. At a time when there is more pressure than ever to be more efficient, more reliable, more productive, more environmentally friendly, and also utilize fewer resources, many organizations are reviewing their lubrication programs to create maintenance-based savings and reduce oil consumption. Using a centrifugal oil separator is the best way to do this.
In this particular case study, the customer approached us eager to see how the IOW centrifuge filter could benefit one of their container ships.
This vessel has a lubricating oil system capacity of 1100 liters. The new IOW centrifuge filter technology extends oil change intervals, reduces the oil consumption and, as a result, this customer could see big savings.
Unlike the traditional centrifugal oil separator, the IOW centrifuge filter range is a newly designed centrifuge filter with brand new patent-protected features. It has been improved to avoid the cross-contamination of clean and dirty oil, contains bowl disc technology that creates a larger surface area for greater separation efficiency, and is the only product of its kind to offer a choice of remote monitoring separator control units (SCUs). These factors provides many advantages to the organization and the engineering team on board.
Having previously used a competitive brand of old centrifugal oil separator technology, this customer was keen to retrofit the new centrifuge filter technology. It was decided for this MAN 9L21/31 engine that the most appropriate choice would be an IOW MP600 engine oil centrifuge filter and CentriClean remote monitoring unit. Designed to be retrofitted to existing pipework, upgrading was easy and quickly showed impressive results!
By using the IOW MP600 centrifugal oil separator, the customer managed to increase the amount of sludge they were removing; from 2.5kg on the old centrifugal oil separator to a jaw-dropping 6kg on the newly installed IOW Group centrifuge filter after just 136 run hours!
With the increased soot collection levels from the IOW MP600 centrifugal oil separator, the question was, what was in the dirt removed from the centrifuge?
Oil samples were taken, and the investigation began to find out what was in the extra sludge cake gathered inside the IOW centrifuge filter. It was determined that due to the effective filtration, the lubrication oil was suitable for continued use and particulate levels were low- all thanks to the IOW centrifugal oil separator.
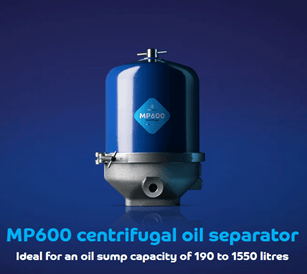
An IOW MP600 centrifugal oil separator
The soot that the IOW centrifuge filter removed could have been extremely harmful and costly in the long run. Lube oil analysis and testing of the IOW centrifuge filter sludge cake showed high levels of asphaltenes.
Asphaltenes are naturally occurring in crude oil. They are large, complex, and heavy carbon molecules and one of the most common foulants in the industry- they contain hundreds or even thousands of chemical species, and are insoluble. Asphaltenes are particularly problematic with regards to corrosion and fouling in an engine, and the deposits of these create process inefficiencies, deteriorate equipment rapidly, and as a result, increase maintenance expense and a loss in production levels. To avoid the deposition of these particles in the equipment they must be efficiently removed.
The IOW MP600 engine oil centrifuge filter successfully highlighted and contained the harmful contaminants avoiding any further damage. Through investigation of the sludge collected in the centrifugal oil separator, engineers were able to correctly diagnose and identify the source of the problem. Without this intervention, the massive quantities of particulate would have caused increased engine wear, maintenance, and overhaul costs in the future.
IOW Group was happy to assist in resolving this ingress of asphaltenes and helping to optimize reliability, productivity, and efficiency onboard this vessel by using an IOW centrifugal oil separator. By moving away from old centrifuge filter technology and opting to upgrade to an IOW centrifuge filter, this customer has extended the life of their engine and lube oil.
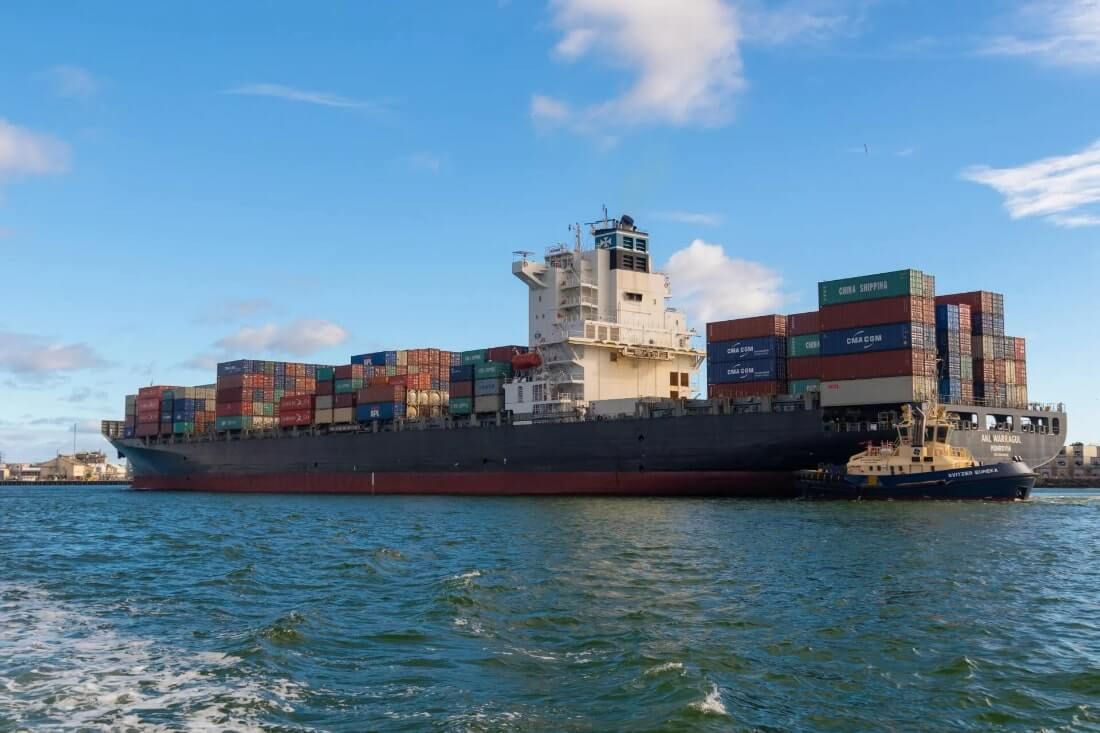
Marine engines have used centrifuge filters to filter lube oil for many years to protect from harmful particles.
Interested in upgrading your lubrication system to the latest and most efficient centrifuge filter technology?
Fill in the contact form and one of our knowledgeable and experienced team members will soon be in touch!
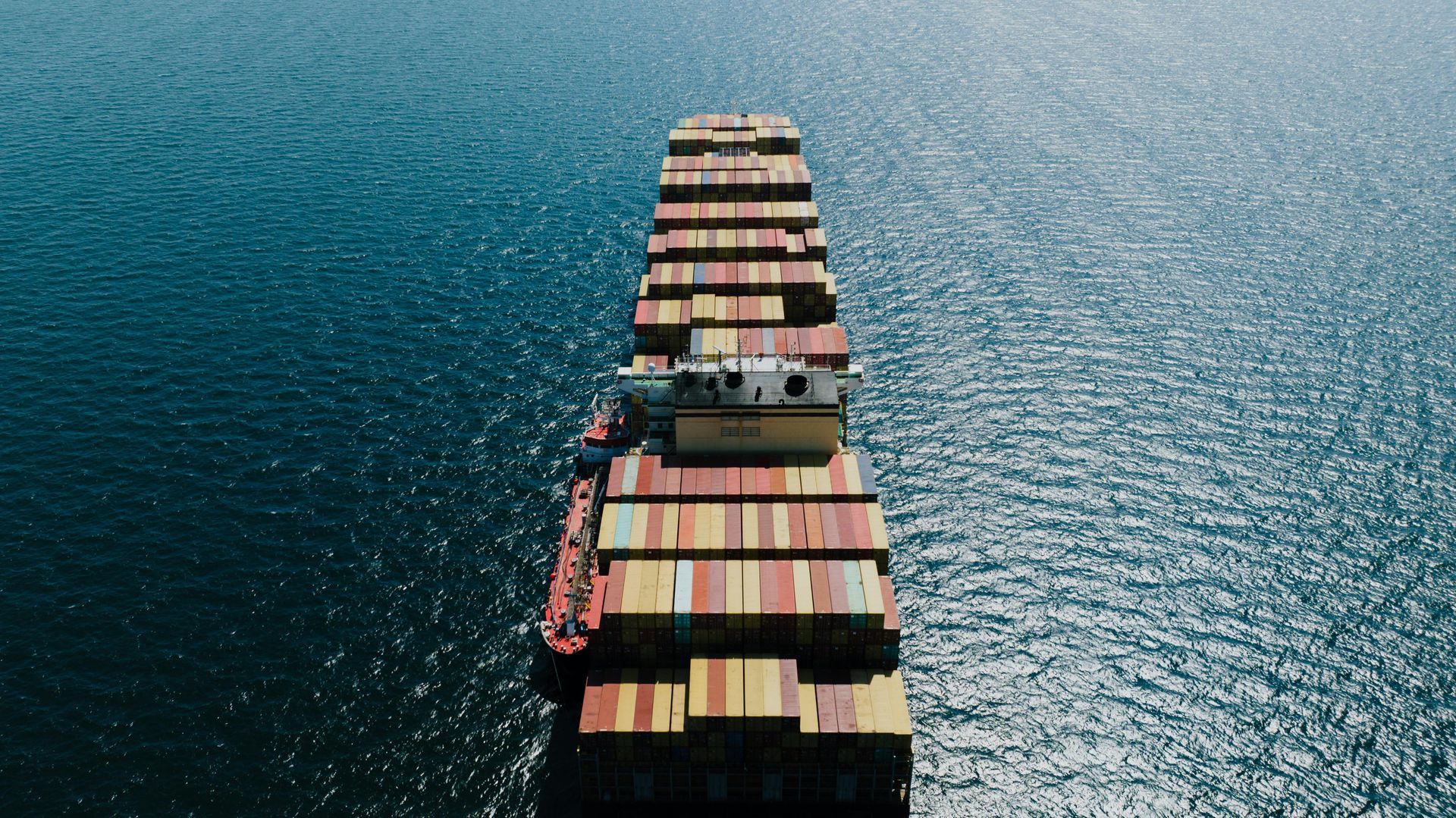
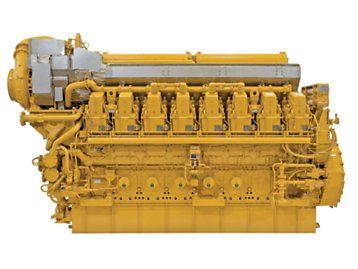